Tesla는 2년전 2020년 9월 배터리데이에서 배터리 가격을 절반으로 낮추는 5가지 언급
1) 주행거리는 +54% 증가
2) 배터리 팩의 kWh 당 비용은 -56% 감소
3) 투자비용은 -69% 절감이 가능
테슬라, 배터리 가격을 절반으로 낮추는 5가지 방법
1) 배터리셀 대형화 및 공정개선,
2) 건식전극 및 고속연속 생산 공정 도입
3) 실리콘 음극활물질 적용
4) 양극활물질에서의 하이-니켈 적용 및 공정 간소화
5) Cell-Vehicle Integration
위 5가지 방법을 통한 비용절감 추진할 것
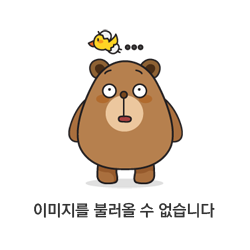
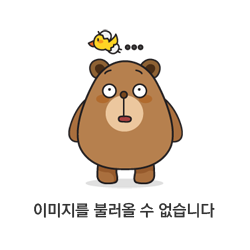
1. 배터리셀 대형화 및 공정개선
배터리 셀 4680 대형화와 탭리스 적용을 통한 공정 개선
테슬라는 원통형 배터리셀 대형화 및 공정개선을 통해주행거리 증가 및 비용 절감을 추진한다
(팩 기준 비용 절감 -14%).
1) 4680 배터리
현재 사용 중인 2170(직경 21mm, 길이 70mm) 원통형 배터리를 4680(직경 46mm, 길이 80mm)으로 크기를 키워 배터리 셀당 에너지밀도를 높이고 생산성을 더욱 최적화할 계획이다.
2) 탭리스(Tabless) 기술
- 공정 간소화 및 연속 생산 공정이 가능해지면서 추가적인 비용 절감이 가능
- 탭이 사라질 경우 기존에 있던 별도 탭을 부착시키기 위한 용접 과정(탭 웰딩)을 거치지 않아도 된다
- 탭리스 기술 적용시 전자 이동거리도 250mm 에서 50mm 로 1/5 줄어들기 때문에 열효율 및 출력도 개선
이를 통해 주행거리가 기존 대비 +16% 증가 예상
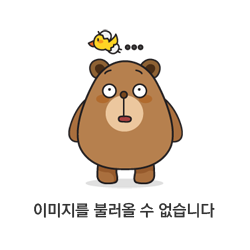
2. 건식전극 및 고속연속 생산 공정 도입
차세대 4680 배터리에 건식전극공정적용할 계획,자체배터리셀 생산캐파구축할예정
1) 새로운 4680배터리에는 건식 전극 및 고속연속생산 공정이 도입될 예정이다(팩 기준 비용 절감 -18%).
기존 습식 공정에서의 용매 휘발 공정이 필요 없기 때문에 원재료 비용 감소 및 공정 간소화, 추가적인 에너지밀도 향상이 가능해진다.
2) 지난 2019 년에 인수한 Hibar Systems 등을 통해 취득한 노하우에 기반해 고속 연속 생산 공정을 도입할 경우 생산 효율을 7 배까지 높일 것.
현재 Tesla 의 배터리 셀 생산은 파일럿 설비를 통해 이루어지고 있지만 1~2 년간의 시험 가동을 거치고 나면 해당 설비에서 10GWh 의 생산능력을 갖추게 된다.
당초 배터리 셀 생산 캐파 규모는 2022 년 100Gwh, 2030 년 3TWh 를 목표로 한다고 언급했지만 지연되고 있는 상황이다.
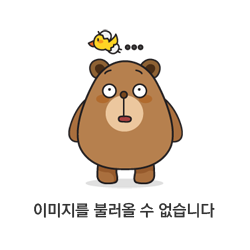
3. 실리콘 음극활물질 적용
실리콘 음극활물질 적용으로 충전시간과 에너지밀도 개선 기대
새로운 형태의 실리콘 음극활물질이 적용될 것으로 보인다(팩 기준 비용 절감 -5%).
실리콘은 음극활물질로 사용되었을 때 흑연 대비 9 배 많은 리튬을 저장하는데 문제는 그만큼 팽창이 쉽게 일어난다.
팽창과 수축을 반복하게 되면 음극재 코팅면이 파괴되고, 리튬 트랩 현상이 발생
지금까지 실리콘을음극재로 활용하기 위해서
1 SiOx(SiO Glass) 적용($6.6/kWh),
2 흑연 구조에 실리콘 적용($10.2/kWh),
3 실리콘 나노와이어 적용(>$100/ kWh) 방안이 고려
Tesla 는 자체적인 공정을 통해 생산한 Tesla Silicon 을 $1.2/ kWh 의 저렴한 비용을 들여 적용
Tesla 는 실리콘 음극활물질을 탄력 및 전도도가 높은 폴리머로 코팅한 후 추가로 팽창문제에 견딜 수 있는 바인더를 사용할 것
4. 양극활물질에서의 하이-니켈 적용 및 공정 간소화
전기차 주행거리 별로 하이-니켈, 코발트 프리, LFP 등 다양한 양극재를 적용한 배터리 사용 계획
양극재에서 하이-니켈 및 코발트-프리(망간-리치) 양극활물질이 적용될 것(팩 기준 비용 절감 -12%).
Tesla 는 차종별로 배터리를 구분
1) Medium range 에서는 LFP(Iron-Based),
2) Medium-Plus 및 Intermediate range 에서는 니켈-망간,
3) Long range 에서는 하이-니켈
적용할 계획이다.
중장기적으로는 양극활물질을 자체 생산할 예정이며 원재료 및 공정 간소화를 통해 투자비의 -66%, 공정 비용의 -76% 감축
5. Cell-Vehicle Integration
배터리셀을더 효율적으로 채워 넣을 수 있는 전기차 플랫폼 개발
Cell-Vehicle Integration, 이는 Cell-to-Chassis 에 가깝다(팩 기준 비용 절감 -7%).
Tesla 는 Single-Piece Casting 을 통한 부품 감소와 공정 간소화를 통해 Rear Underbody 에서 이미 40%의 비용 절감을 이루어냈다.
추가로 모듈과 팩을 생략해 배터리 셀을 기존 대비 더 밀도 있게 차체에 채워 넣음으로써 추가적인 에너지밀도 개선을 이루어냈다.
예를 들면 기존 비행기 날개에 연료통을 따로 탑재하던 방식에서 날개 자체를 연료통으로 사용하는 방식으로 전환하는 것과 비슷하다 볼 수 있다.
Tesla 의 목표는 명확하다.
‘차세대 저비용 고성능 배터리’를 ‘대량 양산’해 세계 최고 수준의 배터리 셀을 자사 전기차에 적용하겠다는 것이다.
기존보다 배터리 셀 크기를 키워 에너지밀도를 높이고 신소재와 공정 효율화를 통해 최종적으로 원가를 56% 낮추겠다는 계획이다
특히 공정 개선을 통한 원가 절감 부분에 대해 강조하고 있다.
Tesla 의 목표가 현실화된다면 배터리 가격이 내연기관차의 Cost parity 로 알려진 $100/kWh 이하도 충분히 가능해져 전기차 가격도 $25,000 수준까지 하락할 것으로 언급했다.
특히소재의변화는모든배터리셀 업체들이가고자하는방향이다.
반면 건식 전극 공정은 에너지 밀도 및 출력저하 등 기술적 난제로 양산 적용이 쉽지 않다고 여겨져 왔다.
20여년간 기술이 발전해 오면서 표준으로 자리 잡은 습식 전극 공정을 대체한다는 것이 상당히 어려운 일인 것은 분명하다.
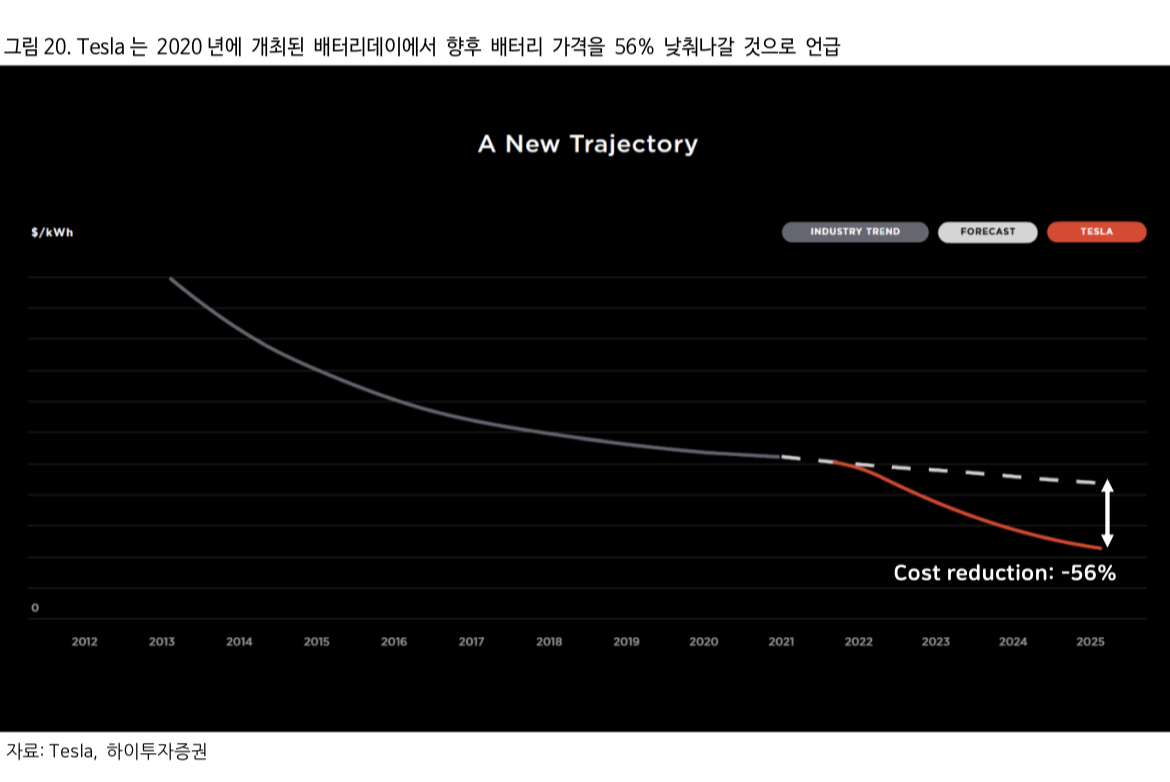
출처. 하이투자증권
배터리 공정 지각변동(feat. 마법의 가루)
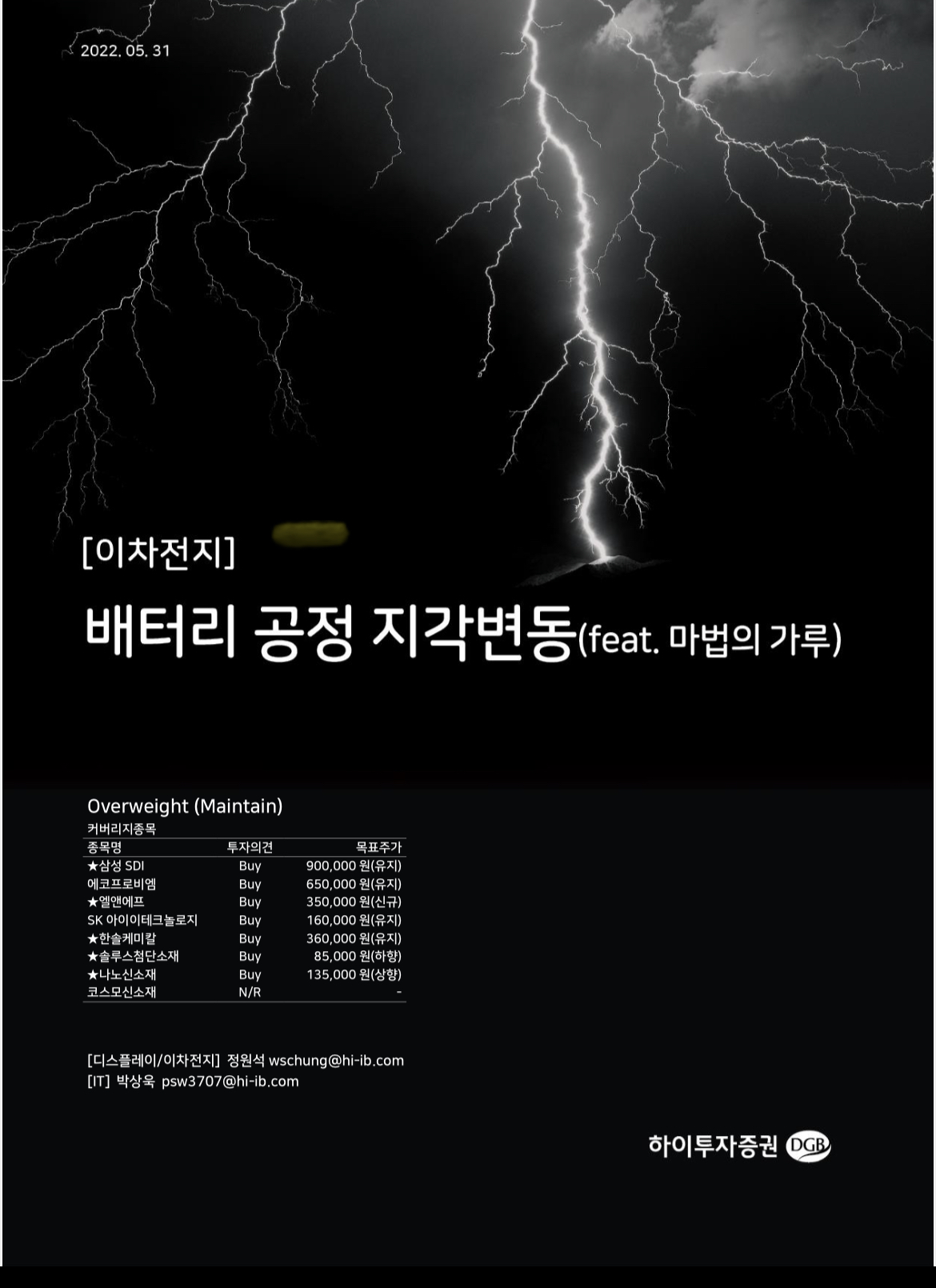